Our
Our technical teams specialise in scalable, cost-driven manufacture of drug delivery devices, specifically for potent API applications. We employ moulding, solvent casting, extrusion and co-extrusion processes, that are developed in our R&D labs, proven in our pilot GMP suites and scaled in our GMP manufacturing facility.
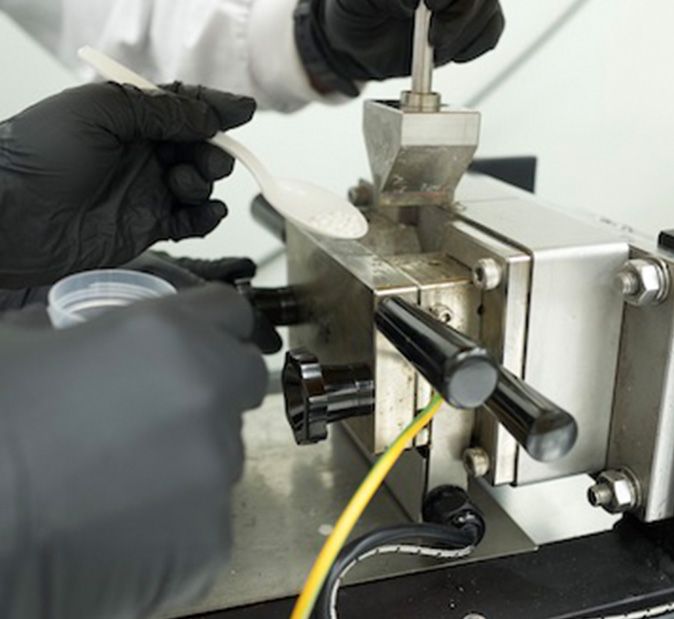
Formulation
and Processing
- Compounding (polymer/drug composite manufacture)
- Batch mixing (30-50g scale)
- Twin-screw extrusion (>500g scale)
- Extrusion
- Twin-screw extrusion (rod profiles)
- Twin-screw co-extrusion (encapsulated rod profiles)
- Moulding
- Injection moulding
- Compression moulding
- Silicone and thermoplastic applications
Development
and Manufacture
- DoE screening of moulded formulations
- Process development
- Analytical development
- Pilot-scale GMP manufacture (up to 50kg batch scale)
- Industrial-scale GMP manufacture (up to 600kg batch scale)
- Packaging
- Labelling
- Large GMP warehouse
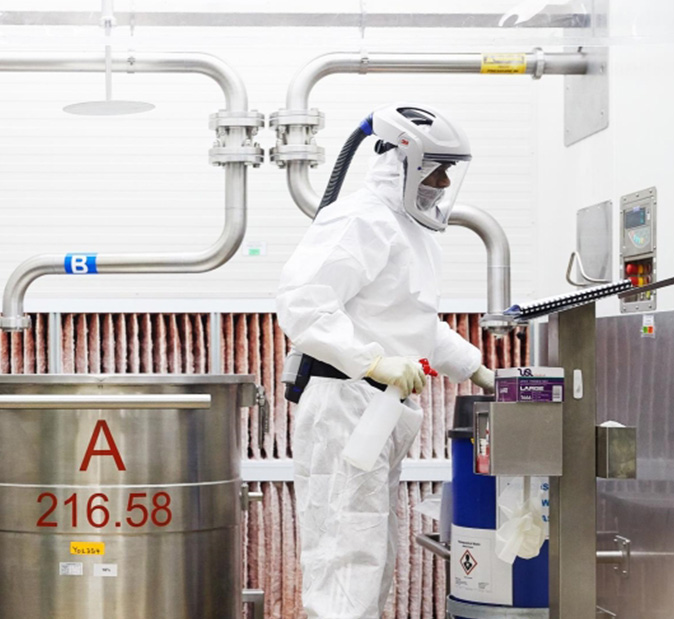
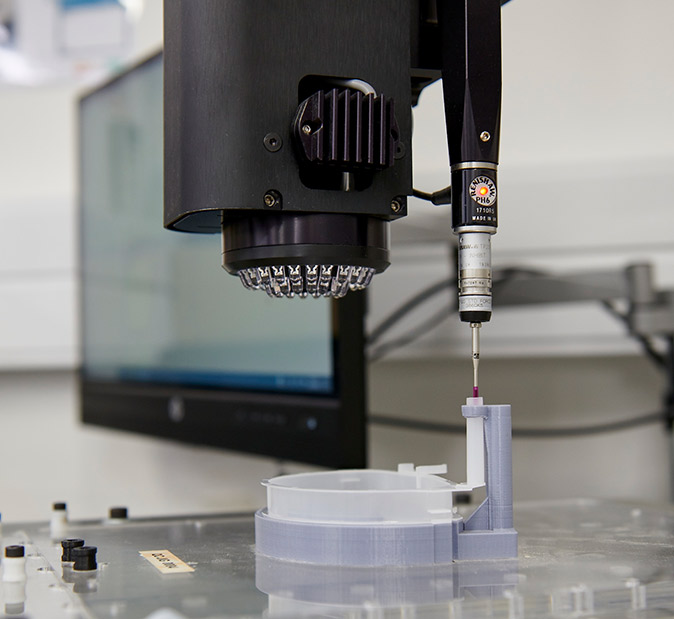
Analytics
- R&D (flexible) and GLP (controlled) Quality teams
- Raw material, in-process and release testing
- Image-based, automated QC measurement (Micro-Vu)
- HPLC, UPLC, UV-Vis, FTIR, (chromatography/spectral analysis)
- DSC (thermal analysis)
- Polarised microscopy (materials and crystallisation analysis)
- Dissolution with autosampling (drug release)
- Sonication or soxhlet (content analysis)
- Mechanical testing
- Stability (intermediate and accelerated chambers)
Quality
- GMP (pharmaceutical)
- FDA registered (currently supplying to >50 countries worldwide)
- NIR in-process control
- Quality by Design (QbD)
- Dedicated Quality Control team
- Dedicated Quality Assurance team
- Equipment Qualification (IQ, OQ, PQ)
- Process validation (process studies, gauge R&R, method validation)
- Tool inspections and refurbishment
- Root cause analysis (RCA, FMEA)
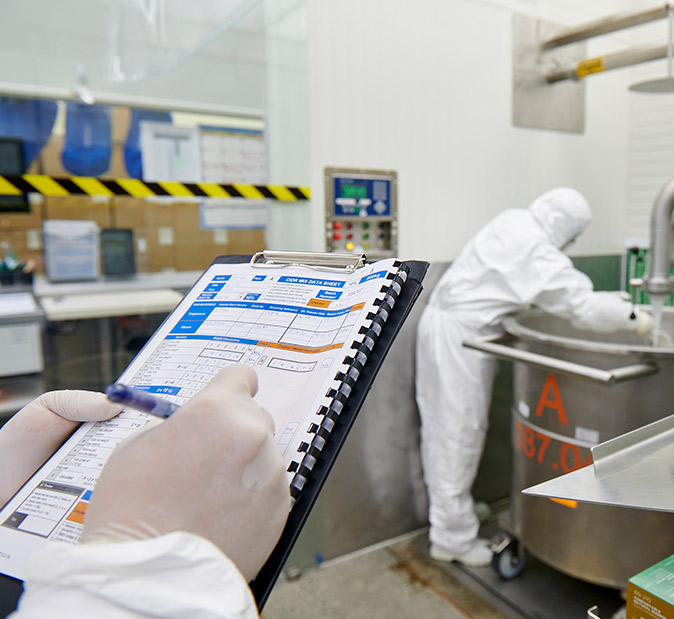